

Comparison of numerical and experimental flow fields at the test section suggests maximum error of 9.84% in case of area-weighted average wind velocity along the length of the test section, whereas along the height of the test section a maximum error of 7.75% is observed. Mass flow rate and pressure jump obtained by system curve are utilized for inlet and outlet boundary conditions, respectively. A novel approach of system curve generation by experimental analysis of wind tunnel is adopted, instead of using the conventional approach of fan-type boundary condition. Boundary conditions have a significant influence on the validation of numerical simulation. For detail assessment of the spatial variation of flow variables, numerical analysis is carried out. Experimental data are collected at different selected locations along the wind tunnel length and inside the test section. The residence time distribution study shows that the presence of screens renders the flow closer to plug flow with the effect being more pronounced using finer mesh screens operating at high flow velocities.Ī numerical and experimental investigation of flow, inside the test section of an open-type subsonic wind tunnel, has been incorporated in the present paper.
Slip screen tunnel how to#
This explains their good performance in processing multiphase flows and gives an insight on how to design systems that maximize this dispersive effect in their volume. These parameters also show that the flow through screens is highly dispersive where 39.3% of the reactor volume has an extensional efficiency value greater than 0.6. The flow field and velocity gradients are interpreted using strain rate and vorticity. Moreover, the presence of the screen has a major impact on the turbulent velocity profile both up- and down-stream. The study shows that the flow through screens is three-dimensional by nature with secondary flows being prominent near the pipe walls. The macro-mixing performance of screen type static mixers is also assessed using residence time distributions. The accuracy of the numerical results is validated by comparing pressure drop predictions to empirical correlations where a maximum relative error of 13.3% is recorded. A three-dimensional computational fluid dynamics model is used to study the effect of changing the operating conditions and reactor configuration on the flow field.
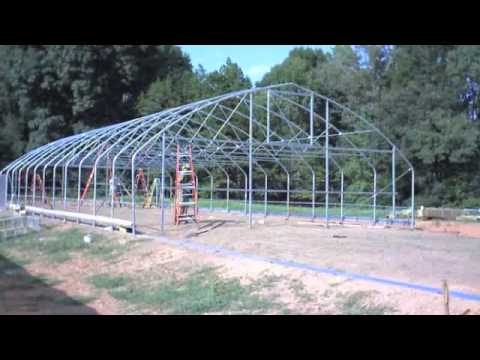
The hydrodynamic performance of turbulent flows in circular pipes equipped with screen- type static mixers is numerically assessed in this study.
